Research and development
Nornickel is one of the smartest companies in Russia. It ranked first among the Top 15 Russian companies by value of intellectual capital (USD 22.4 bn), according to the Baker Tilly accounting and consulting firm.
The Group's main R&D facility is Gipronickel Institute, one of Russia's largest research and engineering hubs for mining, metallurgy, concentration and processing of minerals that develops a wide range of research and technology products.
In 2017, in addition to Gipronickel Institute, the Company used over 35 domestic and foreign research and engineering companies and also Russian universities, including: IPKON (Moscow), Siberian Federal University (Krasnoyarsk), VNIMI (St Petersburg), Outotec (St Petersburg), Norilsk State Industrial Institute (Norilsk), Mekhanobr Engineering (St Petersburg), NPO Atmosfera (Perm), VNIIR (Kazan), MIPT (Moscow), Institute of Chemistry and Technology of Rare Elements and Mineral Raw Materials (Apatity), SPb-Giproshakht (St Petersburg), St Petersburg Mining University (St Petersburg), Uralmekhanobr (Yekaterinburg), RZD Logistics (St Petersburg), etc.
Nornickel's R&D activities mainly focused on research, technological development, and feasibility studies under the Company's updated strategic development plan.
The Company also carried out its operating efficiency programme for 2015–2017 aimed at finding unique solutions to streamline the mining planning process, increase overall recovery rates for nickel, copper, cobalt and PGM, re-process secondary resources (tailings, copper slags, and nickel bearing pyrrhotite with a low nickel content), and optimise the work-in-progress inventory levels. Other programmes included upgrade of nickel and cobalt production technologies at Kola MMC, improvement of product quality and optimisation of production costs.
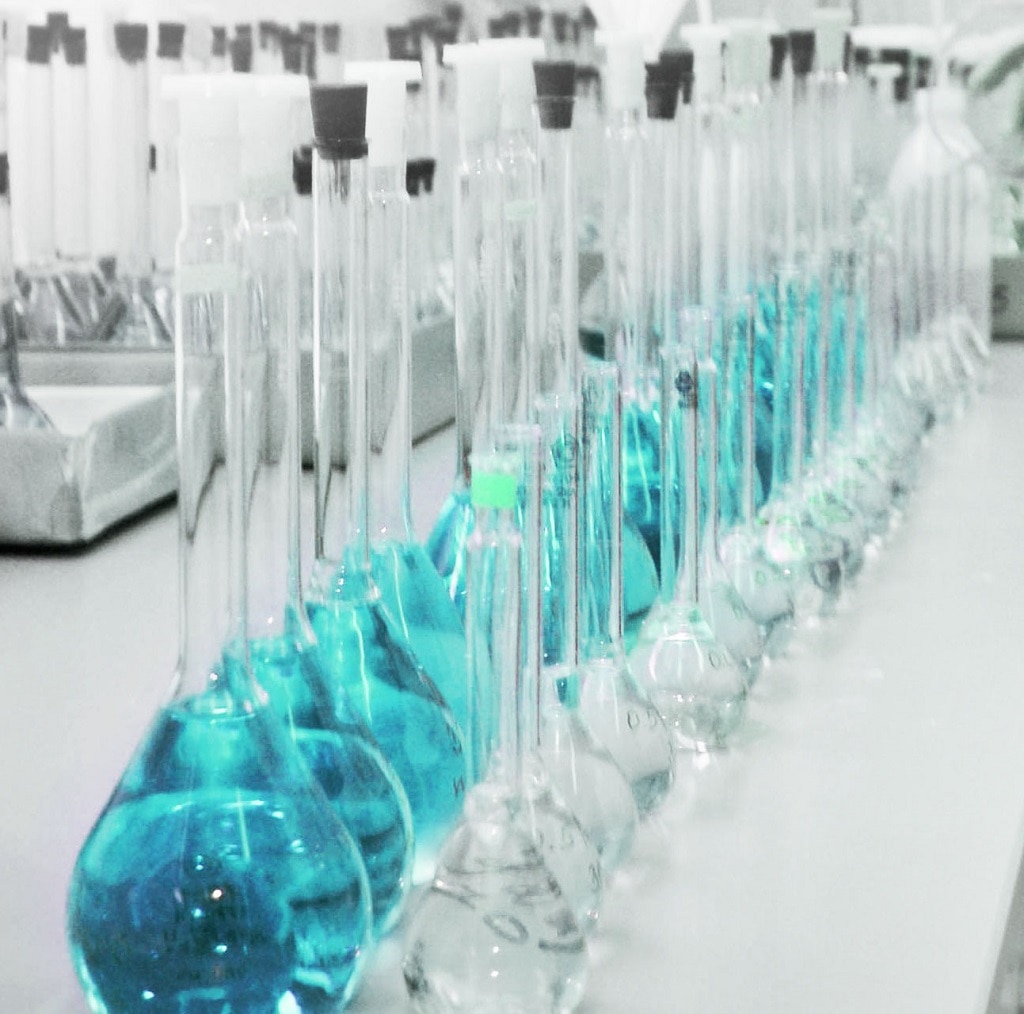
Results in key R&D areas in 2017
- feasibility study to choose the optimal design for the Company’s copper refining facilities (stage 2);
- operating procedures for a feasibility study on refining non-ferrous and precious metals.
Mining:
- adjusted design documents at the mines;
- feasibility study on building an underground crushing section at Skalistaya mine;
- audit of mechanical earth models of Polar Division mines (stage 1);
- feasibility study on using tailings for backfilling on Talnakh mines and on providing Polar Division with limestone and cement.
Concentration:
- project on producing high-grade and low-grade concentrate at Kola MMC’s concentrator and organising shipments of the high-grade concentrate to be accepted and processed at Nadezhda Metallurgical Plant of the Company's Polar Division;
- adjusted operating procedures for ore enrichment at the Bystrinskoye Field;
- adjusted operating procedures for simultaneous processing of disseminated and cuprous ore mixture at Stage 3 of the Talnakh Concentrator.
Smelting:
- adjusted operating procedures to design nickel production facilities at Kola MMC based on the chlorine leaching technology, which will improve the tank-house-2 capacity to 145 ktpa of cathode nickel;
- adjusted operating procedures to design continuous converting facilities at Nadezhda Metallurgical Plant;
- development of operating procedures to design the upgrade of copper production based on the new roast–leach–electrowin technology at Kola MMC;
- development of operating procedures and feasibility study for the process to neutralise sulphuric acid with natural limestone.
- development of operating procedures and feasibility study to produce elemental sulphur;
- inventory of air emissions and development of draft limits for maximum permissible emission at Polar Division’s core production facilities;
- comparison of the technology for producing sulphuric acid and neutralising it with natural limestone vs elemental sulphur production technology used at Nadezhda Metallurgical Plant.